Surface Engineering: Self Healing Thin Films 3: Biomimetic Processes
Dr. Peter Martin
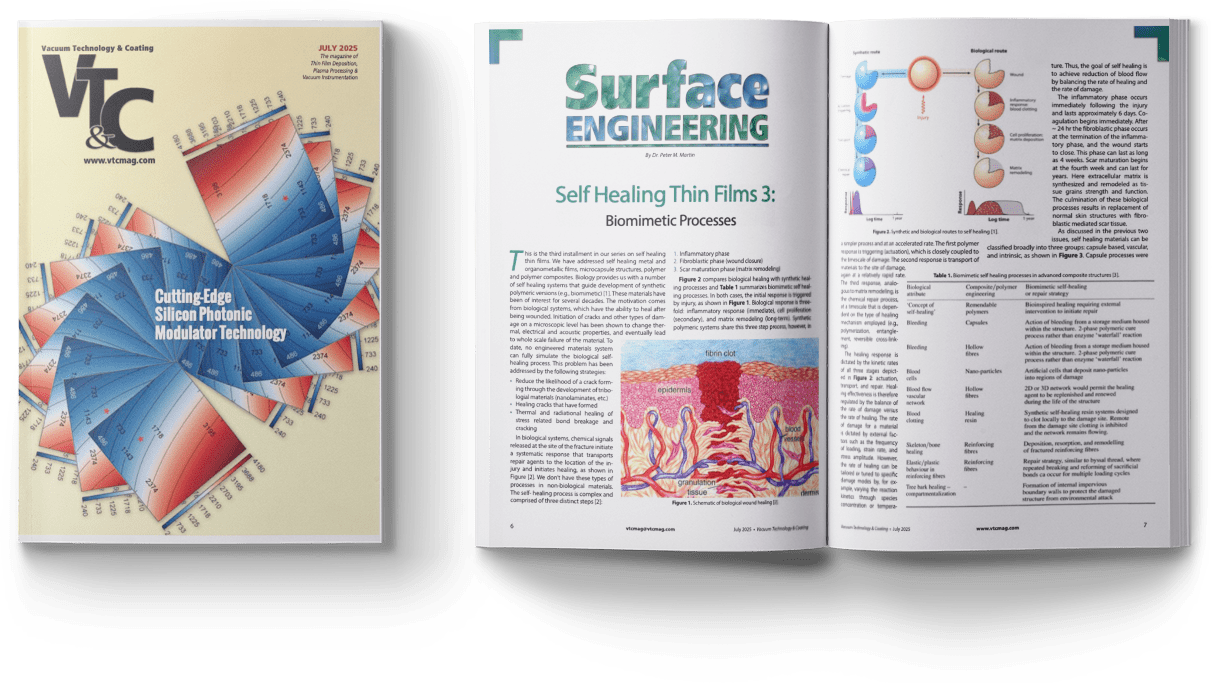
TECHCET— the electronic materials advisory firm—reports that total sputtering target revenues are forecasted to increase ~8.7% in 2025, reaching approximately US$1.45B. This growth reflects a combination of improving demand and metal price appreciation. TECHCET’s wafer start forecast reveals a brief correction is expected in 2028, though overall growth is projected to continue upward through the forecast period. (click for more)
Gentex presented DHF Technical Products with a 2024 Supplier of the Year award at their annual Supplier Conference on May 22nd. DHF Tech was one of 19 suppliers chosen by Gentex for delivering outstanding performance in quality, cost competitiveness, delivery support, innovation and dedication to Gentex. (click for more)
The development of superconducting thin films has opened new avenues in electronic and quantum technologies, offering potential breakthroughs in performance due to their unique properties such as zero electrical DC resistance and perfect diamagnetism. (click for more)
In the high-stakes world of thin film deposition, especially for functional oxides, nitrides and other compounds made by reactive sputtering with metals, precision is everything. For example, slight variations in nitrogen content can impact the color of titanium nitride films dramatically. Figure 1 shows a variation in color, based on nitrogen content, for titanium nitride thin films deposited by reactive sputtering. (click for more)
Since 2000 Vacuum Technology & Coating Magazine has been the industry's leading source for the latest articles, news, and product and service information. Below we describe some of the terms that you will find in a typical issue of VT&C.
Vacuum Coating (Vacuum Deposition and Thin Film Deposition) is the process of depositing a film or other material atom by atom or molecule by molecule onto a surface in a low pressure environment or vacuum.
Physical Vapor Deposition or PVD refers to vacuum deposition methods which involve the material (which is being deposited) going from a condensed phase to a vapor phase and then to a thin film condensed phase. Sputtering and evaporation are common PVD processes.
Sputtering refers to a type of process used to deposit thin films and employs a plasma to bombard and eject atoms from a target source.
Evaporation refers to the heated source material being evaporated in a vacuum. Vacuum allows vapor particles to travel directly to the target object, where they condense back to a solid state. (called a Deposition Source) refers to a type of process used to deposit thin films and employs a plasma to bombard and eject atoms from the target source (called a Deposition Source).
Vacuum Hardware refers to the types of hardware and components that are used in the vacuum process. There are many types of hardware used in this process, some examples are flanges, fittings, seals, valves, and chambers.
Thin Film Metrology involves determining the optimal thickness, composition and/or condition of a coating through various techniques and mathematical calculations.
Gas Analytical Systems are used in the analysis of residual gases within a low pressure environment or vacuum.
Vacuum Pumps are devices that remove gas atoms and molecules for the purpose of leaving behind a partial vacuum. Some examples of types of vacuum pumps are rotary vane pumps, diaphragm pumps, and scroll pumps.
Every issue of VT&C includes a product showcase focused on a specific topic relevant to Vacuum Processing, please see our editorial calendar which lists the topic for each issue.